Finite Element Analysis (FEA): Principles, Applications, and Computational Techniques
- Description
- Curriculum
- Reviews
INTRODUCTION:
Engineering problems frequently involve complex geometries, varying material properties, and multiple interacting forces that cannot be easily resolved using traditional analytical methods. Finite Element Analysis (FEA) is a powerful computational technique that enables engineers and scientists to simulate and analyze how structures, components, and materials behave under various physical conditions. It is widely applied in mechanical, civil, aerospace, automotive, and biomedical engineering to optimize designs, enhance performance, and ensure safety.
This course, Finite Element Analysis (FEA): Principles, Applications, and Computational Techniques, provides a comprehensive foundation in FEA, from theoretical concepts to practical implementation using industry-standard software. Participants will learn how to decompose complex problems into finite elements, apply appropriate boundary conditions, and interpret simulation results to make informed engineering decisions.
The course begins with an introduction to the fundamental principles of FEA, including discretization, element types, and governing equations. As participants progress, they will examine stress-strain relationships, meshing techniques, convergence analysis, and numerical solution methods. A strong emphasis is placed on accuracy and efficiency, ensuring that simulations yield realistic and dependable results.
This course includes hands-on training. Participants will use FEA software such as ANSYS, Abaqus, or SolidWorks Simulation to model real-world engineering problems. They will conduct simulations on structural mechanics, heat transfer, and fluid dynamics, gaining practical experience in defining material properties, applying loads, and evaluating performance metrics.
Advanced topics such as nonlinear analysis, dynamic simulations, and fatigue analysis will be addressed to prepare learners for complex engineering challenges. Participants will also review case studies of FEA applications in industry, including failure analysis, product optimization, and safety compliance testing. Understanding the limitations of FEA and validation techniques is crucial for ensuring accurate predictions and avoiding costly design errors.
By the end of this course, participants will have the knowledge and hands-on experience to apply FEA effectively in engineering projects. Whether you are a structural analyst, design engineer, researcher, or student, this course provides the essential skills needed to harness the power of FEA for simulation-driven design and problem-solving.
COURSE OBJECTIVES:
At the end of this course, participants will be able to:
• Understand the fundamental concepts of Finite Element Analysis (FEA) and its role in engineering simulations.
• Apply discretization techniques to break down complex structures into finite elements.
• Utilize FEA software tools to model, simulate, and analyze engineering problems.
• Perform static, dynamic, and thermal analysis to evaluate structural performance.
• Optimize meshing strategies for accuracy, stability, and computational efficiency.
• Interpret simulation results to assess stress distribution, deformation, and failure risks.
• Implement nonlinear, contact, and fatigue analysis for advanced engineering applications.
Â
COURSE HIGHLIGHT:
Module 1: Fundamentals of Finite Element Analysis
• Introduction to FEA and its applications in engineering
• Understanding stress, strain, and elasticity theories
• The FEA workflow: Pre-processing, solving, and post-processing
• Discretization: Element types, nodes, and degrees of freedom
• Hands-on activity: Setting up a basic FEA model in simulation software
Module 2: Meshing Techniques and Model Accuracy
• Importance of meshing in simulation quality
• Types of elements: 1D (beam), 2D (shell), and 3D (solid) elements
• Mesh refinement techniques: Adaptive meshing and convergence analysis
• Balancing computational cost and solution accuracy
• Practical lab: Meshing a mechanical component for stress analysis
Â
Module 3: Structural Analysis and Material Behavior
• Linear vs. nonlinear static analysis
• Understanding boundary conditions and constraints
• Application of loads: Point loads, distributed loads, thermal loads
• Material models: Isotropic, anisotropic, and composite materials
• Case study: Simulating stress and deformation in a mechanical structure
Module 4: Dynamic Analysis and Vibration Simulation
• Introduction to modal, harmonic, and transient analysis
• Evaluating natural frequencies and mode shapes
• Impact loading and time-dependent responses
• Damping considerations in vibration analysis
• Lab session: Performing a frequency analysis of a machine component
Module 5: Thermal and Multiphysics Simulations
• Heat transfer mechanisms: Conduction, convection, and radiation
• Thermal stress analysis and material expansion effects
• Fluid-structure interaction (FSI) basics
• Coupled field analysis: Thermal, electrical, and mechanical interactions
• Practical exercise: Simulating heat dissipation in an electronic device
Module 6: Nonlinear Analysis and Contact Mechanics
• Geometric nonlinearity: Large deformations and buckling analysis
• Material nonlinearity: Plasticity, creep, and hyperelasticity
• Contact mechanics: Friction, impact, and contact constraints
• Convergence challenges and solution strategies
• Case study: Simulating rubber seal deformation in mechanical assemblies
Module 7: Fatigue Analysis and Failure Prediction
• Introduction to fatigue life estimation and failure theories
• Stress-life (S-N) and strain-life (ε-N) fatigue models.
• Crack propagation analysis and fracture mechanics.
• Reliability assessment in mechanical components.
Â
TARGET AUDIENCE:
This course is designed for professionals, researchers, and students who seek expertise in Finite Element Analysis (FEA) for structural, mechanical, and multiphysics applications, including:
• Mechanical, Civil, and Aerospace Engineers
• Product Designers and Manufacturing Engineers
• Researchers and Academics
• Automotive and Biomedical Engineers
• Graduate Students and Aspiring Simulation Specialists
Â
Â
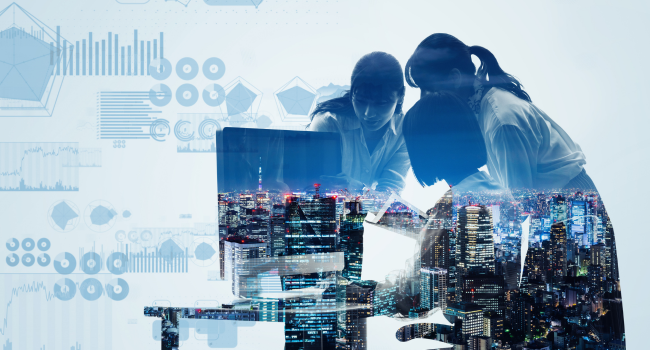